For A 5kw Dc Motor The Number Of Slots Per Pole Should Be
White Papers and Application Notes
Modeling a Brushless DC Motor for an Advanced Actuation System using COMSOL Multiphysics® Software
The number of slots per pole pair should be an odd integer. The number of slots per pole should be at least 9. The number of slots per pole usually lies between 9 and 16. All of the above. An eight pole lap-connected D C motor has 90 slots with four conductor per slot with a speed of 400 r p m calculate the total generated e m f if the useful flux is 0 8wb an electric generator delivers a load current of 24A and a terminal voltage of 250v the generator is driven by a motor whose output power is 7 5kw what is the efficiency of the. Tim Williams, in EMC for Product Designers (Fifth Edition), 2017. 14.2.6.2 Motor suppression. DC brushed motor noise is particularly aggressive, since it consists of impulsive and hence wideband transients repeated at a rate determined by the commutation speed – in other words, several hundred to several thousand times a second. DC MACHINE DESIGN PART 7. PROBLEMS ON SELECTION OF NUMBER OF POLES. A 250 KiloWatt, 500 Volt, 600 R P M, 6 POLE DC GENERATOR IS BUILD WITH AN ARMATURE DIAMETER OF 0.75 Meter AND CORE LENGTH OF 0.3. As you say, in theory the motors should achieve the same max RPM at the same instance. The ESC will have to switch phases 50% more often with the 6-pole motor, but that should not matter since the ESC needs to switch the output anyway, at a much higher rate, to regulate the power to the motor.
This paper presents the design and analysis of a high power radial flux Brushless DC motor for electro-mechanical actuation system. The motor is used for driving an electro-mechanical actuator of 20 ton capacity. Surface mounted, radially magnetized permanent magnet design is mostly preferred due to its ease of control, high efficiency and low maintenance. The motor under consideration is having four set of windings and four set of sensors for redundancy. The motor is rated for a maximum torque of 133Nm (@95A) per winding and a total torque of 532 Nm (@380 A) when all the windings are excited. The speed of the motor is 1850 rpm at a nominal voltage of 270V. The performance evaluation of radially magnetized permanent magnet motors for a three phase, 108 slots, 24 pole BLDC motor was carried out in finite element analysis software COMSOL Multiphysics® software. The number of poles has been chosen such that the motor mechanical envelop has been met and has high efficiency.
Since the motor is used for position control applications, the motor should have minimal cogging torque .In order to achieve this; fractional slot configuration has been chosen. Certain pole slot combinations are preferred. Here 108 slots have been chosen. COMSOL Multiphysics® software (finite element software) is used for computing electromagnetic torque, cogging torque, back EMF, magnetic flux density etc. Inductance calculation by analytical method is difficult and there is no direct relationship also. Moreover the material under consideration is non- linear in nature. So we have done it using Finite element simulation neglecting the end turn leakage inductance.
Inductance is found using energy method and virtual work method, as lower inductance may lead to high torque ripple which is undesirable in servo applications. The specification was achieved during design.
The motor is modeled using COMSOL Multiphysics® software and torque value was found out using Maxwell’s stress tensor method. The air gap flux density is also plotted. There is slight amount of saturation seen in stator core at higher currents in the torque profile, which is expected also. The non linear B-H curve of silicon steel was modeled in finite element software in order to study the saturation effect at high currents. Further reduction in saturation is possible by changing the material to iron cobalt for stator. Due to the presence of the slots, the air gap flux density waveform is having the ripples.
One of the issues faced during the assembly, was the insertion of rotor inside the stator body. The radial force between the stator and rotor handling was difficult. The magnetic pull due to rotor eccentricity was studied and evaluated using finite element method. A fixture is being designed, taking into consideration of radial force.
Download
- ks_paper.pdf - 0.58MB
- ks_abstract.pdf - 0.02MB
White Papers and Application Notes
Modeling a Brushless DC Motor for an Advanced Actuation System using COMSOL Multiphysics® Software
This paper presents the design and analysis of a high power radial flux Brushless DC motor for electro-mechanical actuation system. The motor is used for driving an electro-mechanical actuator of 20 ton capacity. Surface mounted, radially magnetized permanent magnet design is mostly preferred due to its ease of control, high efficiency and low maintenance. The motor under consideration is having four set of windings and four set of sensors for redundancy. The motor is rated for a maximum torque of 133Nm (@95A) per winding and a total torque of 532 Nm (@380 A) when all the windings are excited. The speed of the motor is 1850 rpm at a nominal voltage of 270V. The performance evaluation of radially magnetized permanent magnet motors for a three phase, 108 slots, 24 pole BLDC motor was carried out in finite element analysis software COMSOL Multiphysics® software. The number of poles has been chosen such that the motor mechanical envelop has been met and has high efficiency.
Since the motor is used for position control applications, the motor should have minimal cogging torque .In order to achieve this; fractional slot configuration has been chosen. Certain pole slot combinations are preferred. Here 108 slots have been chosen. COMSOL Multiphysics® software (finite element software) is used for computing electromagnetic torque, cogging torque, back EMF, magnetic flux density etc. Inductance calculation by analytical method is difficult and there is no direct relationship also. Moreover the material under consideration is non- linear in nature. So we have done it using Finite element simulation neglecting the end turn leakage inductance.
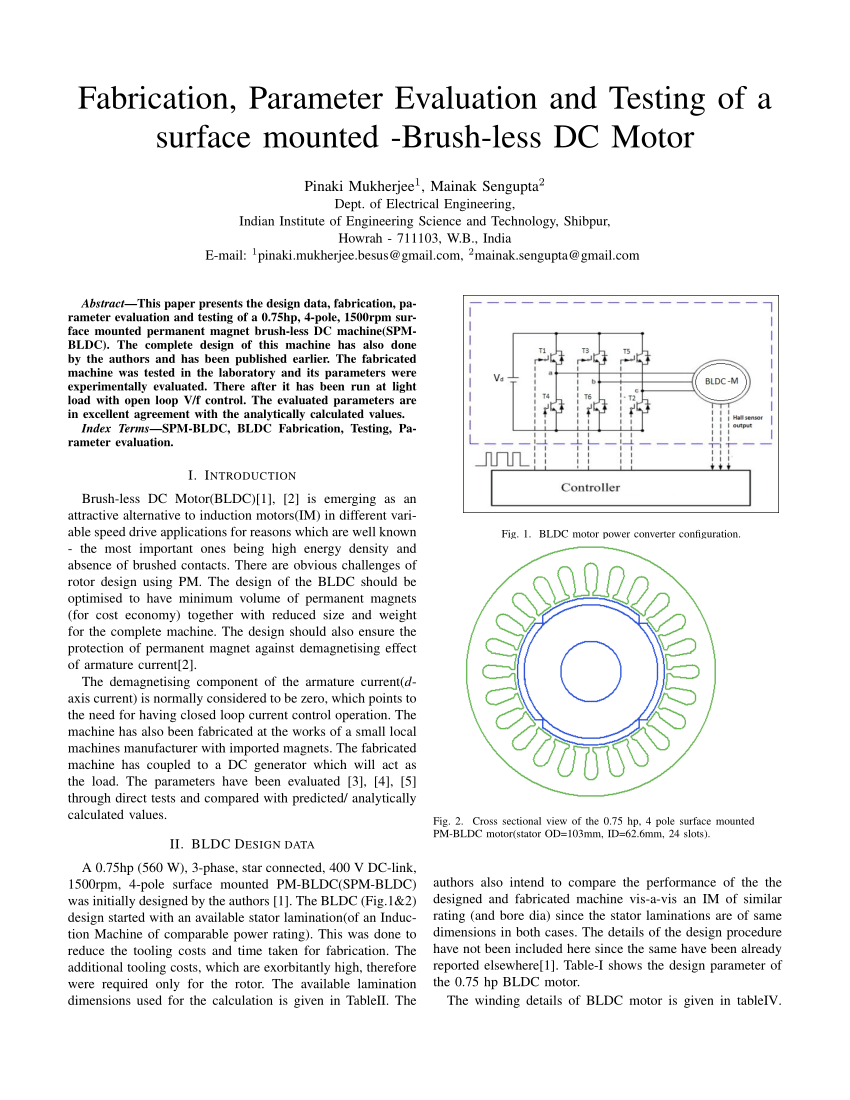
Inductance is found using energy method and virtual work method, as lower inductance may lead to high torque ripple which is undesirable in servo applications. The specification was achieved during design.
The motor is modeled using COMSOL Multiphysics® software and torque value was found out using Maxwell’s stress tensor method. The air gap flux density is also plotted. There is slight amount of saturation seen in stator core at higher currents in the torque profile, which is expected also. The non linear B-H curve of silicon steel was modeled in finite element software in order to study the saturation effect at high currents. Further reduction in saturation is possible by changing the material to iron cobalt for stator. Due to the presence of the slots, the air gap flux density waveform is having the ripples.
One of the issues faced during the assembly, was the insertion of rotor inside the stator body. The radial force between the stator and rotor handling was difficult. The magnetic pull due to rotor eccentricity was studied and evaluated using finite element method. A fixture is being designed, taking into consideration of radial force.
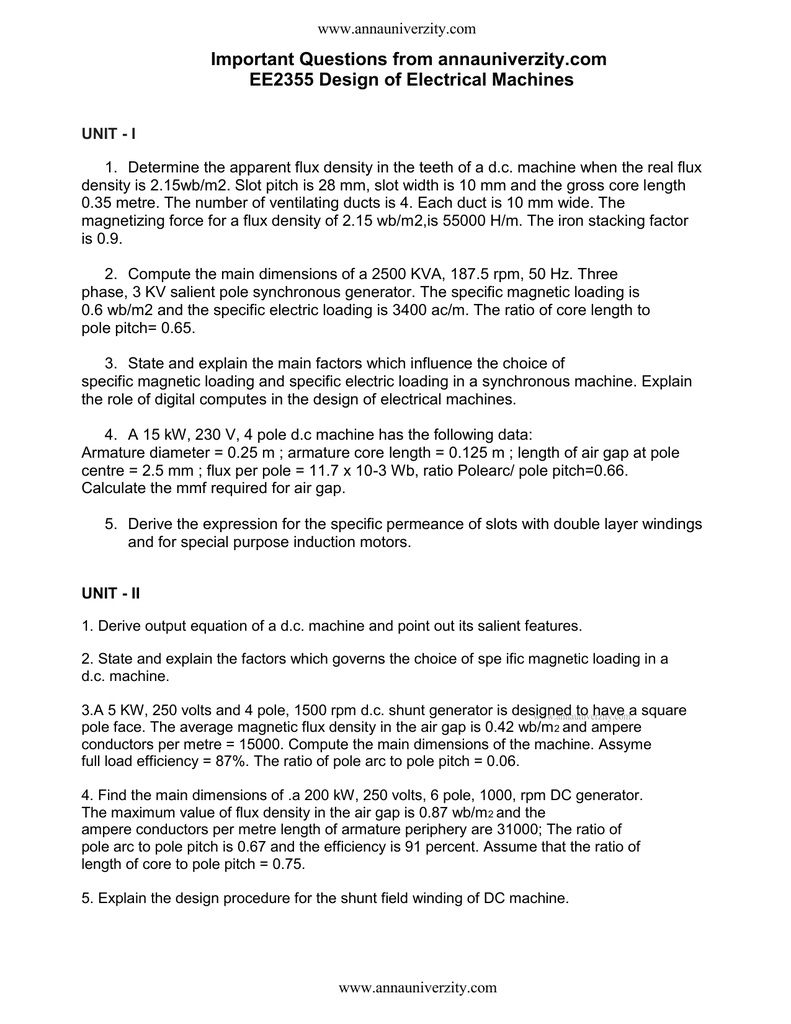
Download
For A 5kw Dc Motor The Number Of Slots Per Pole Should Be Paid
- ks_paper.pdf - 0.58MB
- ks_abstract.pdf - 0.02MB